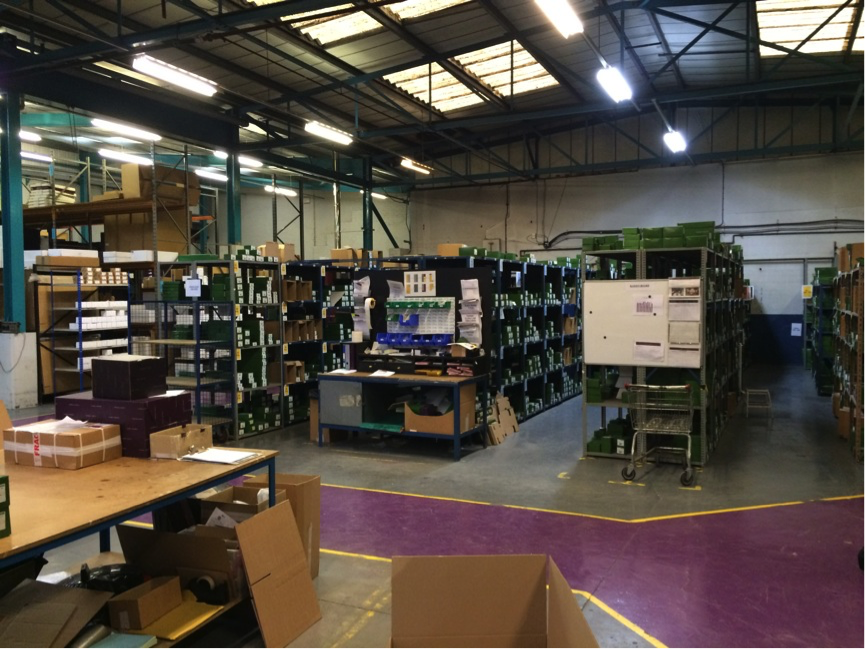
24 Oct Why would you pay for British manufacturing and quality?
I try to champion British products and British craftsmanship whenever I can for our British Georgian interior design schemes. I come up against two issues on a regular basis. The first is the cost of high quality British made product and the second is the often-inconsistent quality that emerges from even the highest end of brands.
So when I find a company whose products are consistently high quality I try to understand what it is that I, or my clients, are paying for and why they are able to deliver consistent standards where so many others fail.
Last week I spent a few hours touring Samuel Heath’s factory. They make brassware; taps, showers and accessories for bathrooms and door and window furniture for the whole house, which blend nicely into Georgian style interiors. And what an eye opener it was.
They are a family owned business that was established in 1820 and they have manufactured their products from the same site in Birmingham, England since 1850.
Not only that, but their entire process is delivered from within that factory which enables them to maintain absolute control over their products. They even make tool parts for their machines so they can be sure of the quality they are working with.
Most products pass through 12 main stages of development, which is what I saw first hand.
1. CAD Design
2. 3D Printing
The product development team use in-house 3D printing for all prototypes. The machines print by layering resin and their output is so precise it passes all the electronic measuring testing used for the end products.
3. Hot Stamping
Wherever the best method is to use time honored skills the traditional method prevails such as hot stamping. Employees at the Samuel Heath factory are in many cases 3rd generation employees.
Hot stamping takes a lump of solid brass, heats it to 1100 degrees centigrade and then places it in a press weighing 5 tonnes to stamp it into shape. You can see the hottest and most recent piece glowing red in the image above. These pieces are going to form part of a door handle.
4. Clipping
After stamping the excess needs clipping. Great care is taken to get the balance between filling the shape entirely and not wasting any metal; so after the clipping process the excess is sent back to the local brass foundry to be melted down and re-used.
Smaller batches are still done by hand using original post-war lathes
5. CNC Machining
The company’s investment in CNC machines deliver hi-tech precision tooling whilst manual labour gives care and attention.
The part below was made in 5 minutes. It is the internal working of a bath filler used to ensure that water is diverted from bath spout to hand held shower. Made out of solid brass with stunning detailing, cheaper imitations may use plastic parts for the interiors that are not seen by the user.
Their entire product range is machined or forged from pure Northern European solid brass made using part recycled material, with the exception of larger spouts which are cast due to the complicated nature of the water flow. This includes internal elements that are precision engineered in brass to ensure longevity and functionality.
The weight of this piece in your hand leaves you in no doubt that you are holding a quality, solid brass part.
The CNC machine that made the diverter
An industrial diamond cutter used in the CNC machine
A huge range of tools are required for the CNC machines as Samuel Heath have such a comprehensive range of products.
6. Recycling
All of the surplus shaving and cuttings of brass are recycled in daily collection.
7. Quality control inspection points
Within each process there is personal responsibility to pass on perfection to the next person in the manufacturing process and automated as well as manual checks are made. I witnessed just how meticulous they are. Ecah stage had pulled out tiny imperfections and set them aside to send back to an earlier process. One spout that had an almost invisible spec on it found at the assembly point was to be stripped back of all the plating layers and re-polished.
Below is a precision tool that measures the part to a tolerance 1/5th of the size of a hair particle.
The cast brass spout above, here in a pre-polished state, has internal parts inserted inside that are made from solid brass, to ensure that there is no chance of a leak which cannot be accessed anytime in the future. A cheaper alternative would not have this.
8. Hand Polishing
These workers are highly skilled and polishing, which is done pre-plating, has four different stages using a finer and finer belt.
9. Plating
State of the art, computer controlled automated plating facility. Great care is taken over the quality and depth of the finish as well as over effluent control
Copper, nickel and then three layers of the finish material – chrome, bronze, nickel etc. plus lacquering if required. The gradual application of several layers, after intense cleaning, ensures the strength of the finished surface which will not crack or peel. Cheaper products have one thicker layer which means the shine is not as high and the layers are not as long lasting.
In total up to 34 processes are undertaken in the polishing and plating of their products to ensure a deep lustrous finish.
10. Assembly
Each part, no matter how small has been made to the highest standard and is assembled with great care.
11. Pressure and temperature testing
All taps and showers are tested for leaks using air pressure which is more onerous than water pressure, and designed to withstand the wide variations of pressure in the 60 countries round the world where Samuel Heath products are sold. Thermostatic units have additional water testing to ensure the temperature is accurate and safe.
12. Warehouse of stock product
A warehouse that looks much like any other ensures that many items are held in stock and can be delivered next day in the UK, most European cities and in New York, and up to 5 days further afield.
Bespoke commissions
Wherever a non-standard product has been developed the in-house design team will liaise direct with the client to produce rapid prototypes and metal samples before production commences
Samuel Heath’s sustainability credentials also became apparent on the tour. Of note was the fact that their raw material brass is sourced no more than 8 miles from their factory; their ceramics are also locally sourced and their packaging comes no more than 15 miles from the factory
Buying British feels good. But sometimes claims that a company’s products are British are only partly true. Some claim that when parts are made abroad and only assembled in Britain.
Companies like Samuel Heath with a 3rd generation workforce and its entire process, from raw material to end product, manufactured in one British factory, deserve the recognition and kudos that that label should denote.
No Comments